Whether it’s for tools, makeup, electronics, or firearms, an aluminum case provides durable, lightweight protection that’s trusted across industries. Behind each sleek and sturdy case is a sophisticated manufacturing process involving advanced techniques and precision engineering. In this post, I’ll walk you through the three main manufacturing methods used by a professional aluminum case manufacturer: CNC machining, die casting, and sheet metal forming. I’ll also touch on several additional forming methods and essential post-processing steps that bring each case to life.
CNC Machining: Precision and Flexibility
CNC (Computer Numerical Control) machining is one of the most precise manufacturing methods for producing aluminum case shells or components. It’s especially ideal for low- to medium-volume production and custom designs.
How it Works:
CNC machines use computer-guided cutting tools to carve out the aluminum from a solid block or sheet. Every movement is pre-programmed with extreme accuracy, down to fractions of a millimeter.
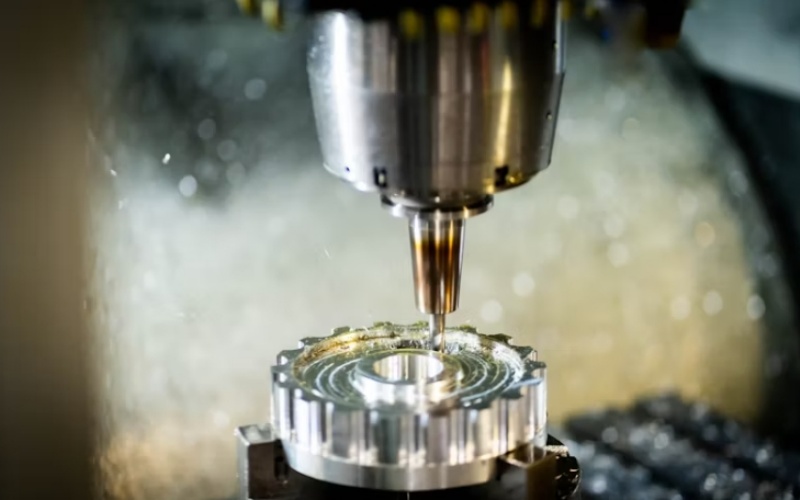
Advantages:
- Precision Engineering: Perfect for parts that need high tolerances, such as locking systems or mounting brackets.
- Custom Designs: Ideal for prototyping or small batch runs where flexibility is key.
- Smooth Surface Finish: Great for applications where visual appeal matters.
Use Case:
An aluminum case manufacturer might use CNC machining to produce handles, corner guards, or even complete compact case shells that require a high-end finish or detailed customization.
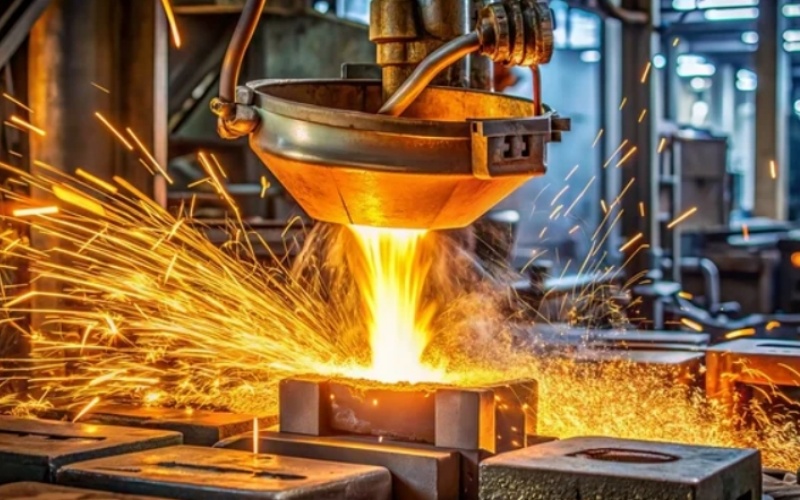
Die Casting: Perfect for High-Volume Production
Die casting is a go-to method when producing large quantities of identical aluminum case shells. It involves injecting molten aluminum into a steel mold under high pressure.
How it Works:
The mold is designed to the exact shape of the case shell or component. Once the aluminum cools and solidifies, the part is ejected from the mold. This allows for quick and repeatable production with excellent consistency.
Advantages:
- High-Speed Production: Ideal for bulk manufacturing of uniform case shells.
- Complex Shapes: Molds can be engineered to form intricate internal geometries.
- Minimal Post-Processing: Surface finish is typically smooth and needs little machining.
Use Case:
Die casting is commonly used for aluminum case shells that require detailed shapes like heat sinks, molded corners, or integrated locking systems.
Sheet Metal Forming: Lightweight and Cost-Effective
Sheet metal forming is the most widely used method by aluminum case manufacturers for building the outer shell. It's economical and efficient, especially for rectangular and box-shaped cases.
How it Works:
Flat aluminum sheets are cut, bent, and shaped into the desired form using hydraulic presses, brake machines, and stamping tools.
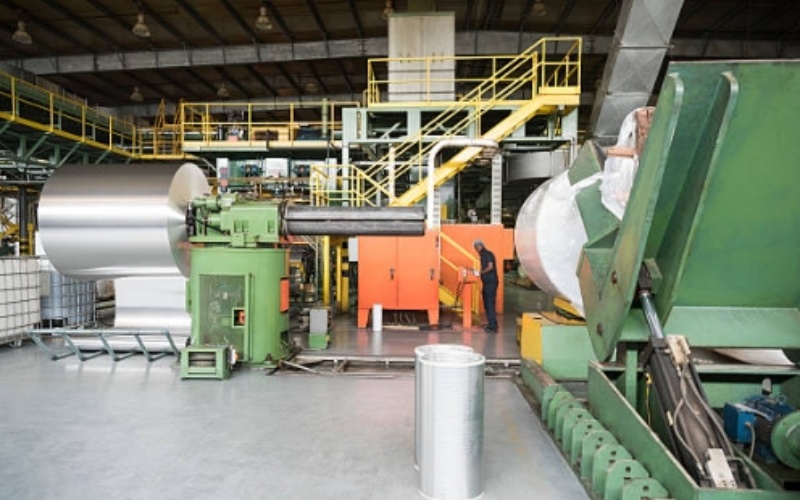
Advantages:
- Cost-Effective: Low material waste and faster forming time.
- Lightweight: Perfect for portable aluminum cases where weight is a concern.
- Scalable: Easily adaptable for both small and large production runs.
Use Case:
Most portable aluminum cases for tools, instruments, or cosmetics are created using sheet metal forming due to its lightweight structure and affordability.
Additional Forming Methods
While CNC machining, die casting, and sheet metal forming are the primary techniques, some aluminum case manufacturers also use complementary methods depending on the design and production goals:
- Extrusion: Used to make long frame components like edges or rails.
- Stamping: Ideal for flat panels and lids, especially in large volumes.
- Deep Drawing: For seamless, box-like shells with greater depth.
- Spinning: Less common, but used for round or cylindrical aluminum containers.
These techniques are often combined with core processes to improve efficiency and meet specific design needs.
Post-Processing and Assembly
Once the aluminum shell is formed, several finishing and assembly steps are carried out to enhance functionality and aesthetics:
Surface Finishing:
- Anodizing: Improves corrosion resistance and can add color.
- Powder Coating: Adds a durable, decorative layer.
- Brushing or Polishing: Provides a matte or glossy appearance.
Accessory Installation:
- Punching/Drilling: Adds holes for hinges, locks, and handles.
- Riveting/Welding: Secures the structure and frame.
- Foam Inserts or Dividers: Installed to protect and organize contents.
Final Thoughts
Every aluminum case you see on the market—from sleek makeup cases to rugged toolboxes—goes through a carefully engineered manufacturing process. Whether it’s CNC machining for precision, die casting for efficiency, or sheet metal forming for affordability, each method serves a unique purpose. As a customer, understanding these methods can help you choose the right aluminum case manufacturer based on your needs—whether you’re looking for custom solutions, high volume production, or a combination of both.
At Lucky Case, we specialize in custom-made aluminum cases with professional-grade finishes and tailored interior options. Whether you need rugged tool cases or stylish makeup organizers, we deliver quality and precision—backed by over 16 years of experience.
Post time: Jul-16-2025